COMPANY INSIGHT
Sponsored by L.B. Bohle
Tablet coating:
problem-free and efficient
Tablet coating represents an important process step in the pharmaceutical solids production. Most coating processes are performed for drug release modification, drug stability improvement against light or moisture and taste masking. Furthermore, patient compliance issues play an important role, as swallowability improvement or a simpler identification via a different color.
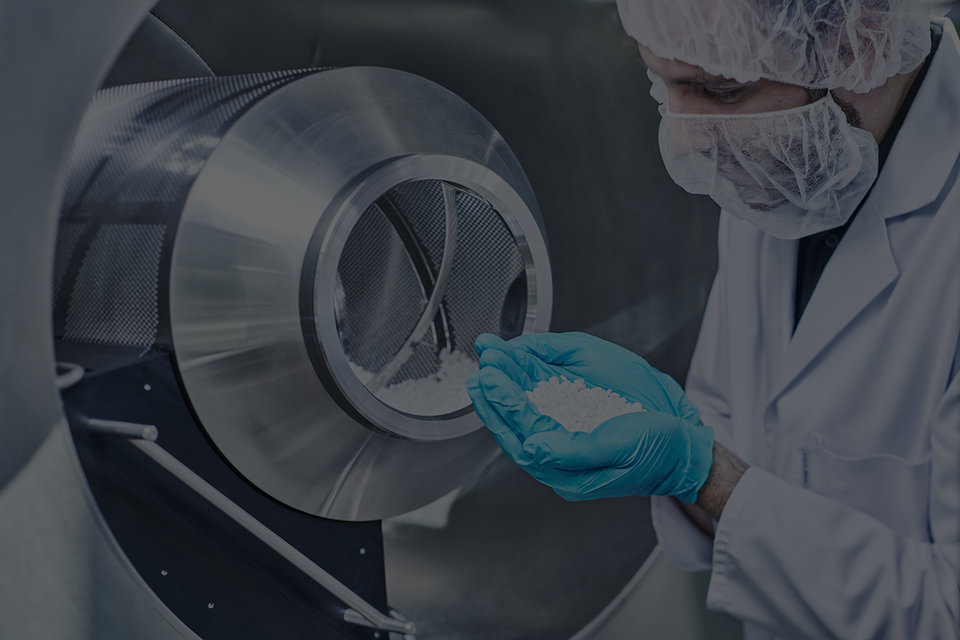
Finally, API coating is gaining more and more importance since it enables fixed dose combinations or the combination of incompatible drugs. Also, different drug release characteristics can be realized by applying for example sustained release coatings in addition to immediate release coating layers. Such formulations consist of up to four coating layers, which leads to long processing times. To successfully develop and produce such formulations coating uniformity is a decisive prerequisite and a quality attribute.
As a coating process consists of simultaneous spraying, mixing and drying processes, a good coating uniformity can only be achieved with the choice of the proper parameters. L.B. Bohle's tablet coaters are setting the benchmark with shortest process times. Furthermore, they ensure best production results and offer the optimal combination on the market.
The perfect synchronization of the following process steps is basically for a successful coating process:
Blending:
It is essential that the tablet cores move evenly underneath the spray cones without mechanically stressing and damaging the tablet cores. The perfect solution for this is an extended coating drum (length to diameter (L/D) > 1) with mixing spirals. The mixing spirals guarantee a constant and gentle mixing of the flat tablet bed. This reduces the mass pressure within the tablet bed. The rotary movement of the coater drum produces radial mixing, resulting in a dead-zone-free tablet bed. Due to the continuous guidance by means of the double spirals, the tablets do not experience strong acceleration, so that tablet breakage or even twinning does not occur.
Spraying:
Due to the drum geometry, the largest possible spray zone is achieved in the moving tablet bed. This allows the use of the optimal number of spray nozzles. Thus, L.B. Bohle Coaters reduce the process time 30 % (approx.) due to higher spray rates compared to conventional coaters. In addition to the suspension, the nozzle type, the number of nozzles and the nozzle-to-tablet-bed distance are important. Bohle offers various solutions for adjusting the nozzle-to-tablet- bed distance, the spray angle of the nozzles and the pressure parameters for atomization.
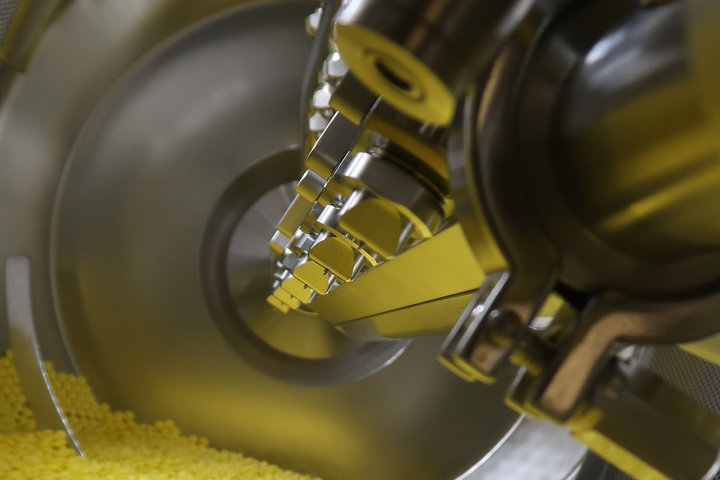
Drying:
All Bohle tablet coaters guarantee best energy and mass transfer through modified air flow. Process air is fed directly into the tablet bed. The air flows directly and smoothly into the tablet bed and ensures fast drying of the sprayed suspension. The spray nozzles are not exposed to the supply air flow for the entire duration of the process, so that they remain cool during the spraying process. As a result, spray drying effects are reduced to a minimum and coating efficiencies of >95 % are achieved. This advantage is also particularly important for active ingredients coatings, as less spray losses and more uniform tablet coatings are produced.
Coating machine for any application
The BFC tablet coater is the high-end version of all coaters from L.B. Bohle and impresses with high efficiency, optimum performance and lowest spray losses. The BFC enables a reduction of the process time by approx. 30 % guaranteeing best coating uniformity. The integrated high-pressure washing system enables Cleaning-In-Place (CIP) with first-class results. Batch sizes of 50-980 liters are possible. Due to geometric similarities, easy scale-up is secured.
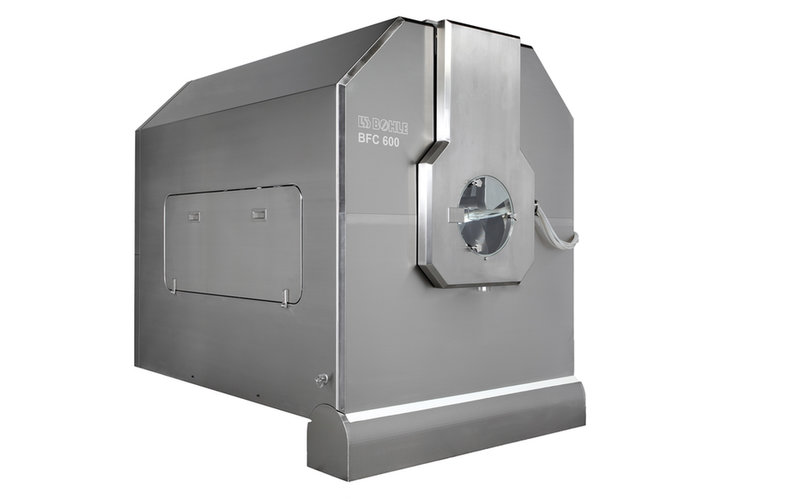
Tablet coating with the high-efficiency BTC guarantees shorter pharmaceutical and nutraceutical processing times compared to conventional tablet coating equipment for significant cost savings and more efficient, longer running operations.
The BFC Tripan is a particularly versatile system that can be operated with three drums. Thus, batches of 7-75 liters can be realized. The drums can be changed easily and quickly.
L.B. Bohle also has the perfect solution for research and development. The BFC 5 laboratory coater is designed as a stand-alone unit and can be operated with two different drums, allowing a batch size range of 2-13 liters.
With the KOCO® continuous coater, L.B. Bohle meets the increased demand for continuous processes. The KOCO® is based on the proven, patented design of all L.B. Bohle tablet coaters and process analysis is carried out via an integrated Raman probe.
Containment - no problem!
The number and scope of containment applications in pharmaceutical solids production has increased significantly in the last years. L.B. Bohle has thus frequently implemented containment solutions for coating applications in all toxicity classes. All containment coaters – whether r&d-scale or production scale is requested - impress with e.g. an automatic nozzle adjustment, infrared product temperature measurement, the connection for cleaning and drying as well as the control integration of the containment valves or side doors with inflatable seals.
Contact information
L.B. Bohle Maschinen und Verfahren GmbH
Industriestraße 18
D-59320 Ennigerloh
Website: lbbohle.com
+49 25 24 93 23-0
Email: info@lbbohle.de