Feature
Cleanroom tech tackles environmental impact of consumables
R&D centres on balancing safety and sustainability across the pharmaceutical sector to design the cleanrooms of tomorrow, writes Natasha Spencer-Jolliffe.
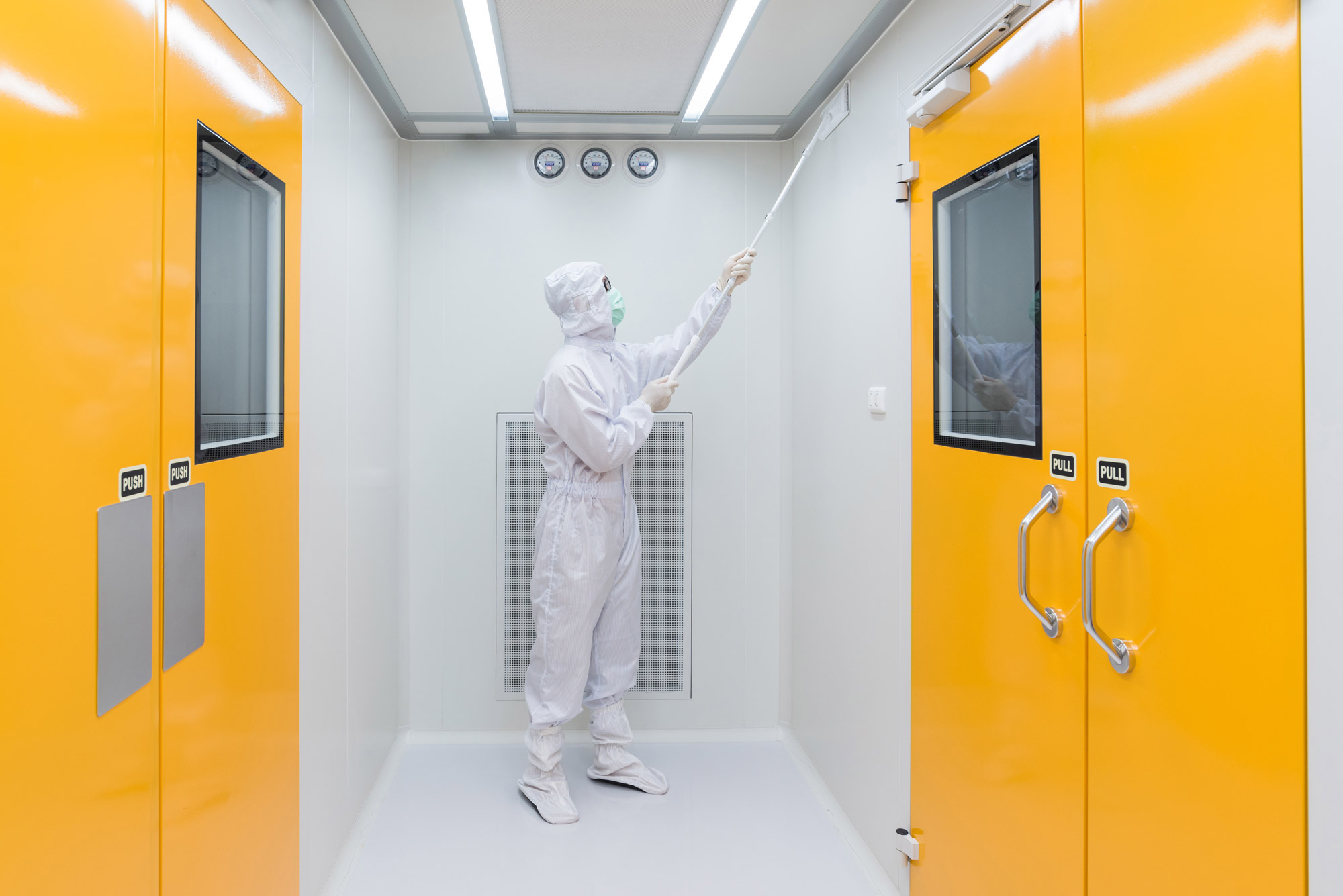
Today’s cleanrooms use equipment and engineering to guarantee low contaminant levels in research and manufacturing facilities. Due to the necessity for minimal contamination, cleanroom technology is prevalent in the production of certain drugs, biologics and vaccines, and hospitals.
Researchers often use single-use consumables like containers, pipettes, and apparel to maintain a sterile environment. Maintaining a balance between minimising the risk of contamination and being environmentally friendly is a challenge. Yet with calls for safety and sustainability increasing in frequency and volume, developers are exploring initiatives to narrow the gap and design cleanrooms for now and the future.
The mine’s concentrator can produce around 240,000 tonnes of ore, including around 26,500 tonnes of rare earth oxides.
Gavin John Lockyer, CEO of Arafura Resources
Australia could be one of the main beneficiaries of this dramatic increase in demand, where private companies and local governments alike are eager to expand the country’s nascent rare earths production. In 2021, Australia produced the fourth-most rare earths in the world. It’s total annual production of 19,958 tonnes remains significantly less than the mammoth 152,407 tonnes produced by China, but a dramatic improvement over the 1,995 tonnes produced domestically in 2011.
The dominance of China in the rare earths space has also encouraged other countries, notably the US, to look further afield for rare earth deposits to diversify their supply of the increasingly vital minerals. With the US eager to ringfence rare earth production within its allies as part of the Inflation Reduction Act, including potentially allowing the Department of Defense to invest in Australian rare earths, there could be an unexpected windfall for Australian rare earths producers.
Total annual production
However, the question remains: can Australia, or indeed any country, develop a rare earths industry independent of Chinese dominance? A raft of new projects and ambitious expansion works could be Australia’s best answer to this conundrum.
The cleanroom design challenge
To meet the particular needs of individual medical environments, cleanrooms are often custom designed to fit exact specifications. Each healthcare process varies. There is a range of different equipment and personnel that also changes depending upon the production stage. “These factors create different contamination control challenges and each cleanroom needs to be tailored for its intended use,” says Dr Tim Sandle, pharmaceutical microbiologist and contamination control expert.
The Covid-19 pandemic has increased the demand for modular cleanrooms in the form of pop-up centres to enable more testing.
“The primary challenge within any cleanroom is people because they are the primary variable,” says Sandle. While consistency can be introduced through good gowning and controlling movements through training, people are the main source of contamination. “The main way to protect critical areas from people is through separative technology, such as the use of isolators,” Sandals continues. Isolators cut out personnel interaction with the product.
“Cleanrooms need to be designed to achieve control as per the maximum occupancy under conditions when all equipment is operating,” adds Sandle. Any weaknesses present, such as the slowing down of air or eddying, need to be overcome. A further consideration is the heat generated from equipment, which can exert an adverse effect on the airflow.
The Covid-19 pandemic has increased the demand for modular cleanrooms in the form of pop-up centres to enable more testing. Some established facilities have also expanded their operations more permanently by increasing the size and scale of their cleanroom operations. Modular cleanrooms also offer flexibility in design, which is important for small-scale or emerging technologies, such as biotechnology.
Making cleanrooms more sustainable
To improve design and create more sustainable cleanrooms, BuildingInformation Modelling (BIM) software has enabled “better development and for different scenarios to be more accurately assessed”, Sandle relays. BIM covers geometry, spatial relationships, light analysis, geographic information, quantities and properties of building components.
Recycled materials for apparel, energy-efficient processes and systems and digital technologies are also coming to the fore. Innovations to reduce stationary use and investments in stainless steel systems with larger capacities that replace single-use systems, decontamination via UV disinfection, and minimising the use of single-use plastics strive to bring eco-consciousness to cleanrooms.
The design and operation of motorised fan units is an important way of controlling cleanroom energy. Advances in microcomputing also allow motors to be dynamically self-adjusting, whereby the airflow adjusts to changes in pressure or to the filter loading. Air adjustment enables the motor to require less energy when the cleanroom is in the static state compared with its in-use state, Sandle details.
Cleanroom companies are also looking at construction materials and their overall carbon footprint. Moreover, many discarded cleanroom products can be recycled. Cleanroom garments, including coveralls, hoods, boot covers, hair nets and masks, can be collected, converted, and resold as bulk plastics or converted into eco-friendly consumer products.

Chemists working in industrial laboratory, wearing protective clothing in the cleanroom. Credit: Getty Images/Westend61
Reducing risk
In a climate with growing cost concerns, the energy consumption of cleanrooms is high. Controlled environments consume around 25 times more energy than non-classified spaces in buildings, Sandle details. “Pharmaceutical companies are seeking to lower their costs in an economic climate of escalating energy costs, and this is the key driver,” says Sandle.
The cleanroom sector’s main focus in incorporating sustainability into its design, however, has been in assessing air change rates. “In some cases, these have been ‘over designed’ and have been set too high based on the nature of the operations,” says Sandle. “A more risk-centric approach, drawing on empirical data from particle count studies, can provide a steady and controlled process for decreasing the rate of air into a cleanroom,” Sandle continues.
The cleanroom sector’s main focus in incorporating sustainability into its design has been in assessing air change rates.
Different design elements appear with dehumidification. “Data suggests that dehumidifying the outside air and combining it with return air leads to a reduction in energy consumption for both cooling and reheating processes,” says Sandle.
However, while this airflow can be modified, this must never be to the detriment of contamination control. In the planning stage, life cycle inventories can balance cost, safety and sustainability. These inventories refer to the “detailed descriptions of what it takes to produce products and the environmental impacts of these steps”, says Evan Griffing, cleanroom researcher and principal consultant at environmental clarity. Based on what laundry operators have told his company, Griffing confirms, “We believe that the cleanrooms are motivated to consider sustainability.”