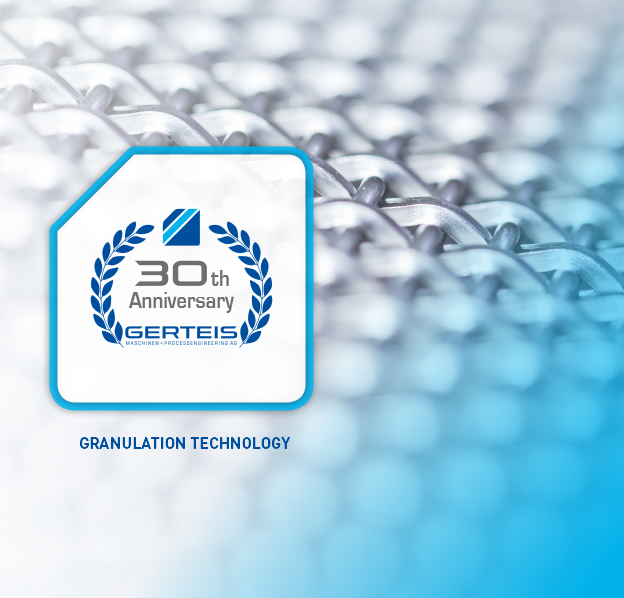
Roller Compaction Technology Increasingly Important For Production Of Granules
Roller compaction is becoming an increasingly important agglomeration technology for the production of granules, as the pharmaceutical industry looks at ways in which it can introduce lean manufacturing to reduce its R&D and manufacturing costs.
GERTEIS® is a Swiss manufacturer of advanced high-quality roller compactors. GERTEIS® has set the standard with its unique dry granulation technology. The company’s understanding of the dry granulation process combined with patented roller compaction systems make GERTEIS® the technology leader in the field of dry granulation.
GERTEIS® has a depth of dry granulation knowledge and experience; its team of roller compaction specialists can evaluate an application and quickly predict and establish the best roller compaction parameters to achieve the optimum dry granulation process.
Gerteis Maschinen + Processengineering AG is the optimal solution for your dry granulation needs. From R&D trials to continuous manufacturing, Gerteis roller compactors can process powders, even those with extremely poor flow properties, far better than any other machine on the market, without the need for vacuum deaeration or roller cooling.
The Pactor line, which can be upgraded with High Containment as well as CIP for potent compounds, represent the best machines to launch a QbD program. Linear scale-up from R&D to high volume production has never been easier due to Gerteis’ sophisticated roller design.
In addition to any required Technical support, Gerteis is pleased to provide Formulation support to all of its customers.
Our product portfolio includes machines capable of product output ranging from 10g per trial up to 400kg / h.
Roller Compaction: Process Analytical Tools
The GERTEIS® roller compactors are able to control and measure all product quality relevant parameters (e.g. force, gap and roll speed) on-line in order to fulfill the requirements of the pharmaceutical industry for a well controlled and documented manufacturing process.
The GERTEIS® roller compactors are able to control and measure all product quality relevant parameters (e.g. force, gap and roll speed) on-line in order to fulfill the requirements of the pharmaceutical industry for a well controlled and documented manufacturing process. All the parameters are calibrated and validated. Additionally, in order to cope with batch to batch variations, our machines are fitted with control systems to allow equal granule properties during manufacturing according to PAT.
GERTEIS MASCHINEN + PROCESSENGINEERING AG had its beginnings as a one-man enterprise in Jona, Switzerland where the corporate headquarters is located to this day. Throughout the years the company grew exponentially and established itself as the market leader for premium dry granulation equipment. With our focus on roller compactors, we pride ourselves in possessing an in-depth knowledge on all aspects of dry granulation and the related processes which is much to the benefit of our customers.
Customer Success Story
Nucleo Life Sciences is a modern and state-of-the-art contract development & research lab (CRO) based in San Rafael, CA covering all phases of small molecule drug product development.
The founders have a long history of using the Gerteis line of pharmaceutical roller compactors for developing and
scaling up high volume pharmaceutical products at various manufacturing plants all over the world.
Pharmaceutical roller compaction is an efficient dry granulation process used to make increase the particle size of poorly flowing powders by compacting into a ribbon or compact. This compacted blend is then milled to increase the
particle size and producing blend that is free flowing and suitable for tablet compression, capsule filling, or filling
into sachets. Gerteis is a Swiss manufacturer of advanced high-quality roller compactor and has set the global
standard with their unique design of dry granulation technology.
“When we moved our lab from San Francisco to San Rafael the Gerteis Mini-Pactor was the first piece of equipment installed in the pilot plant,”recalls Mark Menning, PhD, CEO of
Nucleo Life Sciences. “Having the proper equipment in our facility allows us to perform our prototyping then produce GMP supplies using the same equipment. If the product scales up to a larger batch size or a commercial
facility, we can simply take the recipes in house then transfer it directly to the contract manufacturer (CMO).”
“When selecting equipment vendors, customer support is a critical part of the relationship,” said Lara Park Menning,
COO of Nucleo Life Sciences. “We prioritize client support in our company so we expect the same level of support
and passion from our equipment partners. Gerteis has always exceeded with their technical expertise and
support. Their machines are indestructible with high performance output.”
Pharmaceutical roller compaction is becoming an increasingly important agglomeration technology for the
production of granules, as the pharmaceutical industry looks at ways in which it can introduce lean manufacturing to reduce its R&D and manufacturing costs by QbD.
For any further information please contact Gerteis via sales@gerteis.com or visit www.gerteis.com.
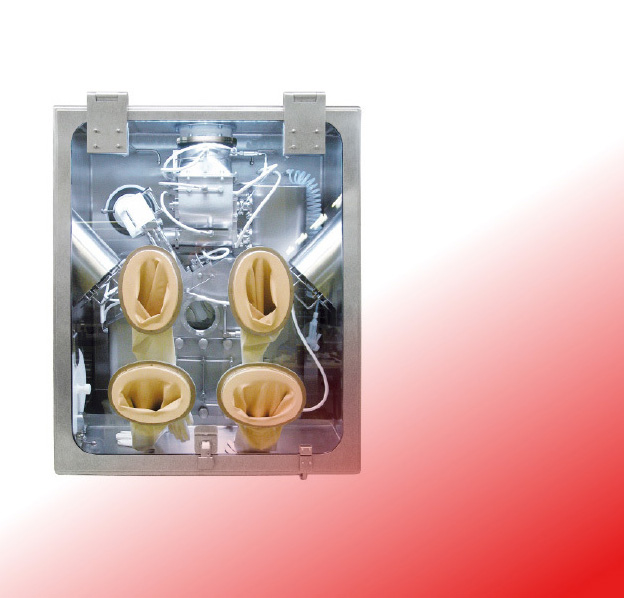
ULTRA-PACTOR® High Containment Roller Compactor
The ULTRA-PACTOR® High Containment Roller Compactor is the most technologically advanced roller compactor for optimal protection from highly active and hazardous substances.
High Containment Roller Compactor
The ULTRA-PACTOR® High Containment Roller Compactor is designed for full Cleaning-In-Place, so that operator contact with hazardous products is completely avoided. The ULTRA-PACTOR® roller compactor guarantees optimal protection for the operator against highly active and hazardous substances. With its ATEX-compliancy and the ability to purge N2 into the process area, this roller compactor truly pushes the boundaries in containment installations for dry granulation applications.
ULTRA-PRACTOR® is the most technologically advanced roller compactor that Gerteis® has produced. Building upon the well proven MACRO-PACTOR® - and with output capacities up to 400kg per hour - the ULTRA-PACTOR® is designed within an ergonomic containment isolator to allow processing of very potent products where high containment is required. In accordance with high containment good practice, the ULTRA-PACTOR® roller compactor is
ULTRA-PACTOR® Roller Compactor Features:
- Containment performance of <0.1 µg/m³>
- Ergonomically designed high containment isolator for the highest operator safety
- RTP ports for optimised operator handling
- Push-push filter designs
- Permanent online pressure monitoring for all seals and pressure zones
- Fully automatic Cleaning in Place
Roller Compaction Options
- Different roller surfaces
- Different granulator designs
- Built in PAT control system
- MES interface
- Variable screen mesh sizes
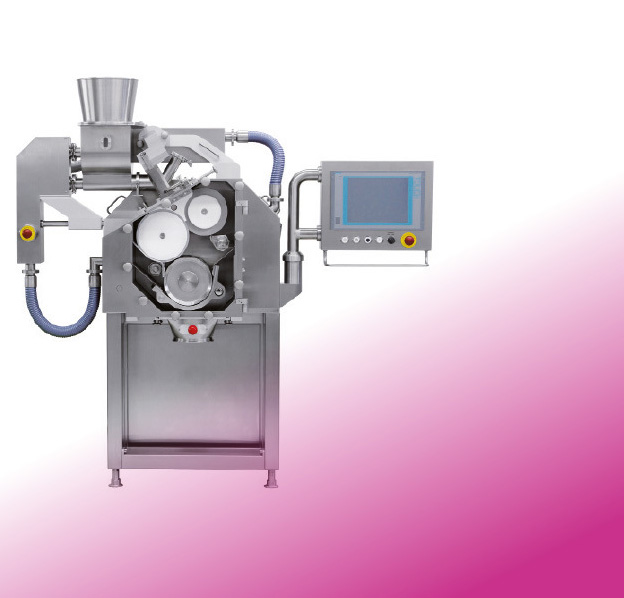
MACRO-PACTOR® Roller Compactor
Advanced Dry Granulation Technology
The MACRO-PACTOR® is the premium Gerteis® roller compactor with output capacity of up to 400kg per hour. However, as a fully continuous granulation process, amounts from as little of 100g can also be dry granulated, making the MACRO-PACTOR® suitable for development and pilot scale environments. Complete harmonisation with the other roller compactors within the PACTOR® range is assured with identical roller diameters. The result is that scale-up is straightforward, avoiding common problems associated with batch based processes, reducing material and API costs, and saving time to get the product to market quicker.
Unique Gerteis® Roller Compaction features
- Consistent feed system to the rollers with torque control of the screw feeder and tamp auger to ensure precision dosing of powder
- Angled compaction rollers to allow feed consistency, constant ribbon density and to minimise temperature gain.
- Free floating gap design and in-process force control producing a constant density ribbon
- Large diameter rollers to produce a longer dwell time in the nip area.
- Superior punch & die roller design to provide a constant density over the ribbon width and to virtually eliminate fines (no recirculation required!)
- Three stage milling process with the granulating oscillating mill with adjustable screen clearance, to produce a consistent and controllable particle size distribution.
- Full instrumentation with critical quality process parameter data-acquisition
- Full machine calibration
- Standard containment performance of 3 µg/m³ Time Weighted Average
MACRO-PACTOR® Roller Compactor Options
- WIP/CIP cleaning,
- Enhanced containment performance
- Build in PAT control systems
- Press roller cooling/heating
- Vacuum de-aeration.
- Different roller surface designs
- Separate feed funnel for small quantities.
- Industrial PC solutions
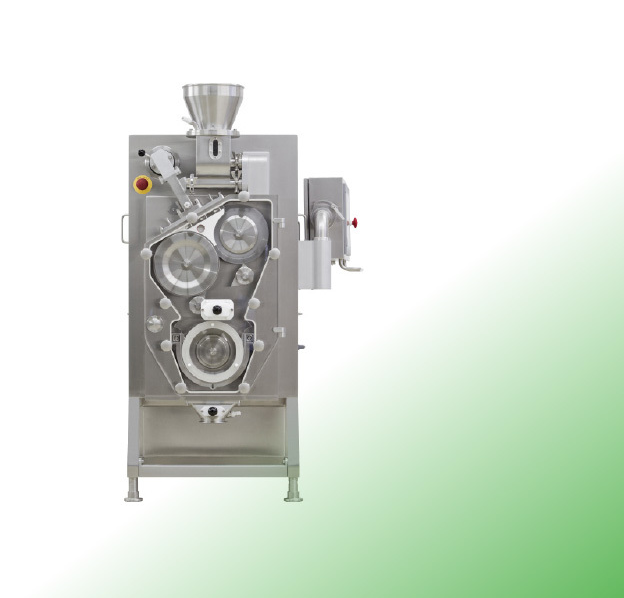
MINI-PACTOR® Roller Compactor
Advanced Dry Granulation Technology
The MINI-PACTOR® Roller Compactor is designed for both laboratory development and for small to medium scale production runs. Roller Compaction is a fully continuous granulation technology; the MINI-PACTOR® has capacities from 10 grams per trial up to 100kg per hour, and with harmonisation with the other PACTOR® designs by having identical roller diameters, scale-up is simple and quick, avoiding risks and reducing costs.
Unique Gerteis® Roller Compaction features
- Consistent feed system to the rollers with torque control of the screw feeder and tamp auger to ensure precision dosing of powder
- Angled compaction rollers to allow feed consistency, constant ribbon density and to minimise temperature gain.
- Free floating gap design and in-process force control producing a constant density ribbon
- Large diameter rollers to produce a longer dwell time in the nip area.
- Superior punch & die roller design to provide a constant density over the ribbon width and to virtually eliminate fines (no recirculation required!)
- Three stage milling process with the granulating oscillating mill with adjustable screen clearance, to produce a consistent and controllable particle size distribution.
- Full instrumentation with critical quality process parameter data-acquisition
- Full machine calibration
- Standard containment performance of 3 µg/m³ Time Weighted Average
MINI-PACTOR® Roller Compactor Options
- WIP/CIP cleaning,
- Enhanced containment performance
- Build in PAT control systems
- Press roller cooling/heating
- Vacuum de-aeration.
- Different roller surface designs
- Separate feed funnel for small quantities.
- Industrial PC solutions
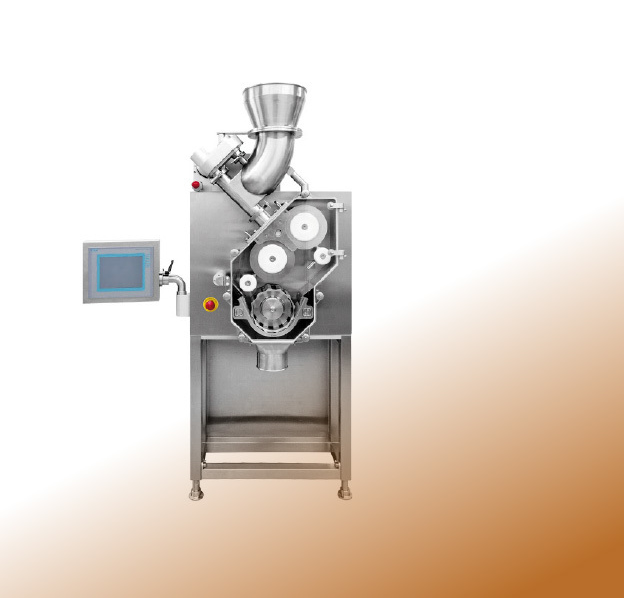
POLYGRAN® Roller Compactor
The POLYGRAN® roller compactor offers outstanding value for money for such a sophisticated roller compactor that will deliver excellent dry granulation results.
Leaders in Roller Compactors
The POLYGRAN® roller compactor is the entry level Gerteis® roller compactor. The POLYGRAN® roller compactor is suitable for both development and production environments. This unique roller compactor features simplified handling and controls for an even easier accessibility. Maintaining the machine is effortless and an ideal machine for medium production quantities with a throughput of up to 300kg/h.
With many of the unique roller compactor technologies of the PACTOR® range included, the POLYGRAN® offers outstanding value for money for such a sophisticated roller compactor that will deliver excellent dry granulation results. With a capacity of 500g up to 300 kg per hour, the POLYGRAN® is suitable for both development and production environments.
POLYGRAN® Roller Compactor Features:
- Simple but accurate feed system to the rollers to ensure consistent dosing of powder to the rollers.
- Angled compaction rollers to allow feed consistency, constant ribbon density and to minimise temperature gain.
- Free floating gap design and in-process force control producing a constant density ribbon
- Large rollers diameters to produce a longer dwell time in the nip area.
- Simple but effective granulating oscillating mill with adjustable screen clearance, to produce a consistent and controllable particle size distribution.
- Full instrumentation with critical quality process parameter data-acquisition.
- Full machine calibration.
- Reduced number of interchangeable parts for easy disassembly and reassembly.
POLYGRAN® Roller Compaction Options:
- Different roller surfaces
- Variable screen meash sizes
- Operator interface with toruch screen panel
- Recipe managment
- Process data archiving
- CFR 21 Part 11 compliancy
- OPC-Connections
- Integrated 2-step granulation system
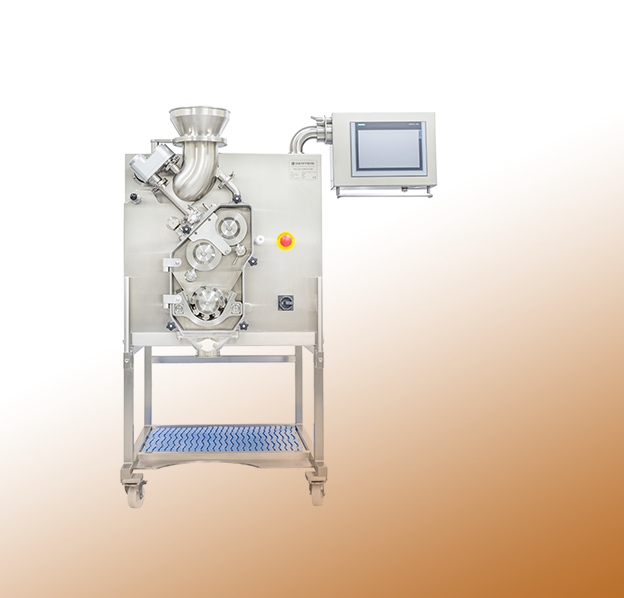
MINI-POLYGRAN® Roller Compactor
The MINI-POLYGRAN® roller compactor combines the ground-breaking GERTEIS® technology with an unprecedented mobility for roller compactors, making this roller compactor the perfect balance between performance and flexibility for your laboratory. The MINI-POLYGRAN® is the ideal roller compactor for laboratory development due to its capacity from 10 grams per trial up to 50kg/h.
Changeover from batch to batch can be completed in one of the industry’s fastest, due to the unique POLYGRAN® - setup of individual machine parts. Scale-up to production volumes can equally be achieved instantly and hassle-free.
Features & Benefits:
- Constant ribbon properties
- Controlled force and gap adjustment
- Fully instrumented
- New feeding system guarantees a constant powder feed per batch
- Validated force and gap measurement
- Longer dwell times due to the large roll diameter
- Constant product quality and properties
- Reduced Parts for rapid changeover and cleaning procedures
- Virtually no heat build-up with the Gerteis® patented roller design
- Convenient placement within the laboratory
- Easy scale-up to production batches
- Ideal for pharmaceutical, food and chemical laboratories
MINI-POLYGRAN® Roller Compactor Options:
- WIP cleaning
- Vacuum deaeration
- Different roller surfaces
- Integrated 2-step granulation system
- Separate feed funnel for small quantities
- Operator interface with industrial PC solutions
INTERPHEX JAPAN
Japan
27th – 29th June 2018
PMEC India
India Expo Centre, Delhi NCR, India
26 – 28 November 2019
Pharmtech Moscow
Crocus Expo IEC, Hall 2 Moscow, Russia
19 – 22 November 2019
Interphex USA
Jacob Javits Center, Booth #1952, New York, USA
2 – 4 April 2019
ACHEMA GERMANY
Hall 3.0 D25
11th – 15th June 2018
INTERPHEX USA
Booth 1952
17th – 19th April 2018
Roller Compaction Seminars
The 2018 Gerteis roller compaction seminars have been a great success. Both seminars were held in September at Gerteis Jona with an international group of attendees. The first seminar in 2018 with the title 'Understanding Roller Compaction Technology' covered all aspects of roller compaction. Starting from the machine setup via the process parameter and trouble shooting. The second seminar 'First Roller Compaction Trials in Development of Dry Granulates' covered the basics for roller compaction development work, scale up and other related topics. All participants had hands on experience with the Gerteis development roller compactor and the production roller compactor during the seminars. We are happy to have hosted many interesting professionals from the industry and to provide an extensive insight into Gerteis’ dry granulation technology. We thank all our guests for their engaging participation and we look forward to see all again in 2019. We would like to thank our guest speakers from the industry as well.
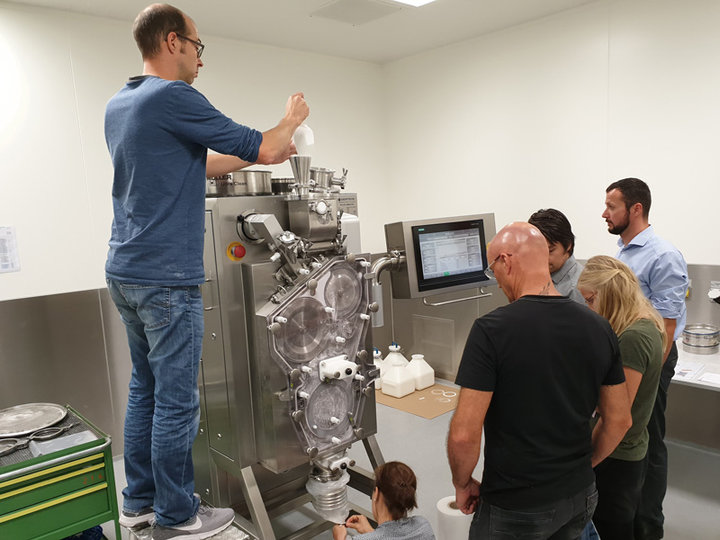
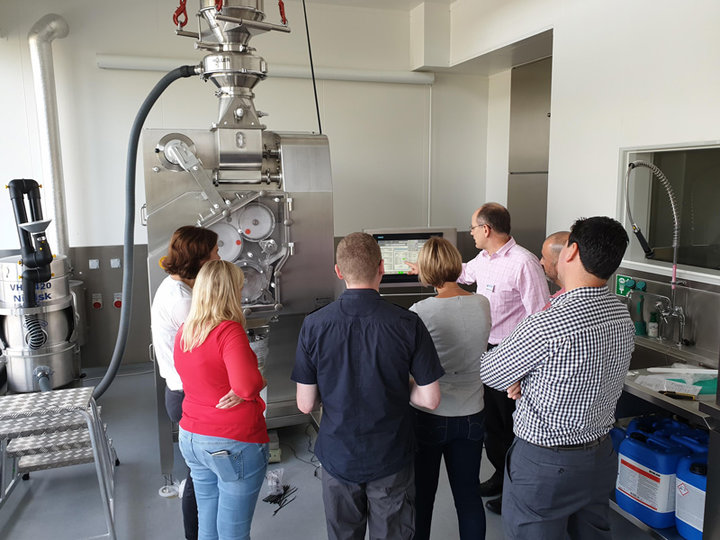
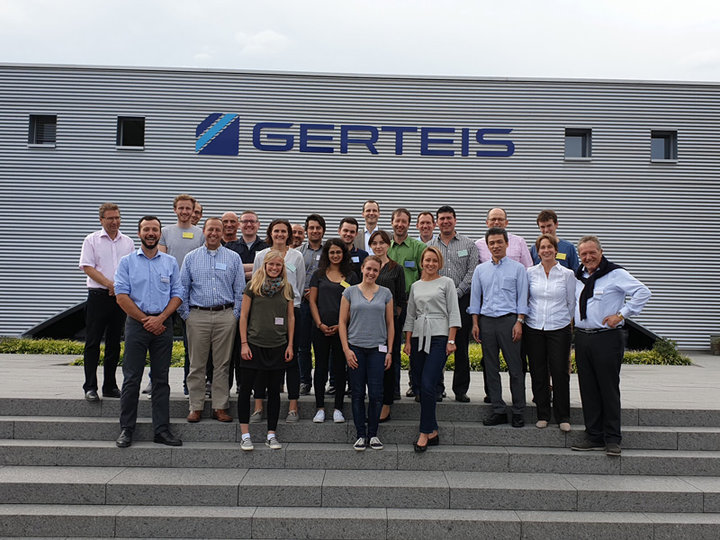