Policy
Discussing drug policy reform with psychedelics campaigner Amanda Feilding
Amanda Feilding has dedicated her life to campaigning to amend global policies towards illegal drugs by conducting scientific research into the medical benefits of cannabis and psychedelics through her NGO, the Beckley Foundation. Allie Nawrat talks to Feilding about the medicinal potential of these compounds and progress towards their legalisation on this basis.
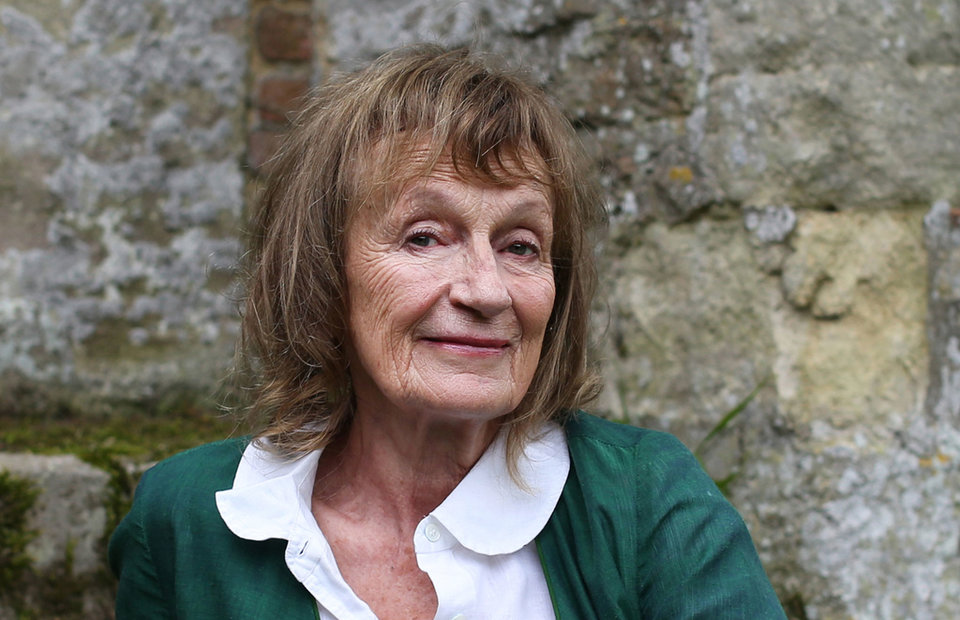
Amanda Feilding has spent the last 50 years campaigning to amend drug policies.
Image courtesy of Imogen Freeland
How could psychedelic drugs transform treatment of mental health patients?
One of our core research projects has been on psilocybin, or magic mushrooms, as a new treatment for the underlying cause of depression, which has a high suicide rate. We found that 67% of patients were depression-free one week after treatment and 42% remained in remission three months later. The psychedelic works by shaking up the rigid, ruminative thought patterns associated with depression.
We are aiming to put products through Phase I, II and then III clinical trials; for psychedelics, this will take a few years, but it would be lovely if it could be sped up to bring benefits to patients with a large need. Research is ongoing, but psychedelics have been shown to be promising potential treatments for otherwise hard-to-treat conditions, such as depression, existential anxiety, addiction and PTSD.
How significant was the UK’s recent move towards legalising medical marijuana?
It is a step in the right direction. However, unfortunately, it has been highly restricted and the actual number of prescriptions is very low, around six. This is because the patient has to prove that no other medication works, which means long periods of medications with nasty side effects, and at the moment only a few specialists can prescribe medicinal cannabis.
Therefore, although the law has changed, major barriers remain, preventing access for patients who would benefit greatly from this medicine. These patients continue to suffer unnecessarily, so changing this needs to be the next priority.
We need to educate our doctors on this topic. There is a gap in their knowledge as cannabis has been illegal and not used medically in the UK for over 90 years. They are cautious and nervous about stepping out of line.
Hopefully, we will follow Portugal, who used to be at the top of lists of deaths and overdoses from illegal drugs in Europe – now the UK is at the top of the list – however, since decriminalising drugs in 2001, there has been a reduction of both drug-related deaths and rates of addiction in Portugal.
Have you noticed a change in public and governmental perceptions towards the potential of prohibited drugs as medical products? What are the remaining barriers to widespread reform of illegal drug policy?
There is an out-of-date perception that these compounds are very damaging and addictive. However, there has been a shift because, as a culture, we are in the midst of a mental health epidemic; there are very high figures of youth suicide, as well as rising rates of depression, which is very worrying.
There is a growing awareness of the efficacy of cannabis and psychedelic drugs in this regard and how they could represent a paradigm shift. People are also increasingly dissatisfied with the existing pharmaceutical and therapeutic approaches as they have low rates of efficacy, significant side effects and often take weeks to kick in. In addition, even if they do work, they only suppress symptoms, not the underlying causes of the disease.
One major remaining barrier is the structure of the UN, which has not changed its perspective on illegal drugs as a taboo, which makes research very difficult and more expensive.
The criminal activity associated with illegal drugs plays into the traditional perception. We do not want criminals and cartels in control of these compounds. We want to create carefully regulated markets in the hands of licensed professionals that mean the products can pass pharmaceutical regulations.
The situation we have at the moment is like the Wild West and is a lose-lose situation. But recently the World Health Organization recommended that cannabis and its key compounds be formally rescheduled under international drug treaties and be removed from Schedule IV – the most restrictive category of the 1961 UN drug convention. We are turning a corner to create a win-win situation.
Go to top